Lean Management
Lean Management is a production methodology that aims to optimize processes while minimizing waste.
Initially developed in the automotive industry by Toyota factories in the 1970s, this inventory management method has since been extended to all types of industries, businesses and services.
The essence of Lean Management lies in the elimination of waste, while focusing on the creation of value. This is achieved by optimally coordinating all company processes.
Waste is any activity that consumes resources without adding value for the end customer.
The 7 wastes identified by Lean management
Lean Management mainly tracks seven types of waste in manufacturing practices:
- Overproduction: Producing more than necessary or in advance of customer demand, resulting in unnecessary stock build-up.
- Excess stock: caused by an unprocessed inventory, this is an unnecessary surplus of materials or products.
- Waiting time: Time lost when production slows down or stops in one stage while waiting for a previous stage to be completed, affecting the fluidity of processes.
- Transport: Unnecessary movement of materials that adds no direct value to the manufacturing process.
- Over-processing : Investing more work than necessary in production, beyond what the customer values.
- Movement: Unnecessary movement of workers or machines.
- Defects: Defects lead to rework or, in the worst case, scrap.
An approach aligned with business and customer needs
Introducing Lean Management into a value chain aims to improve the production system from two angles: that of the company and that of the customer. The aim is to align these two perspectives perfectly.
In this way, Lean Management is in line with the principles of Agile methods, the main aim of which is to optimally meet customer expectations using tools such as cycles and feedback, while avoiding unnecessary development.
Lean Management models
There are several models you can use to implement Lean Management, including:
- The Kanban model: A pull-flow production system, where production is determined by customer orders, following the just-in-time principle.
- The 5S method: An approach to improving organization and efficiency in the workplace.
Thanks to these tools, Lean Management makes it possible to optimize production processes while responding precisely to customer needs, avoiding unnecessary waste and maximizing overall satisfaction.
Unleash your organization's potential.
We're here to answer all your questions and support you in your projects.
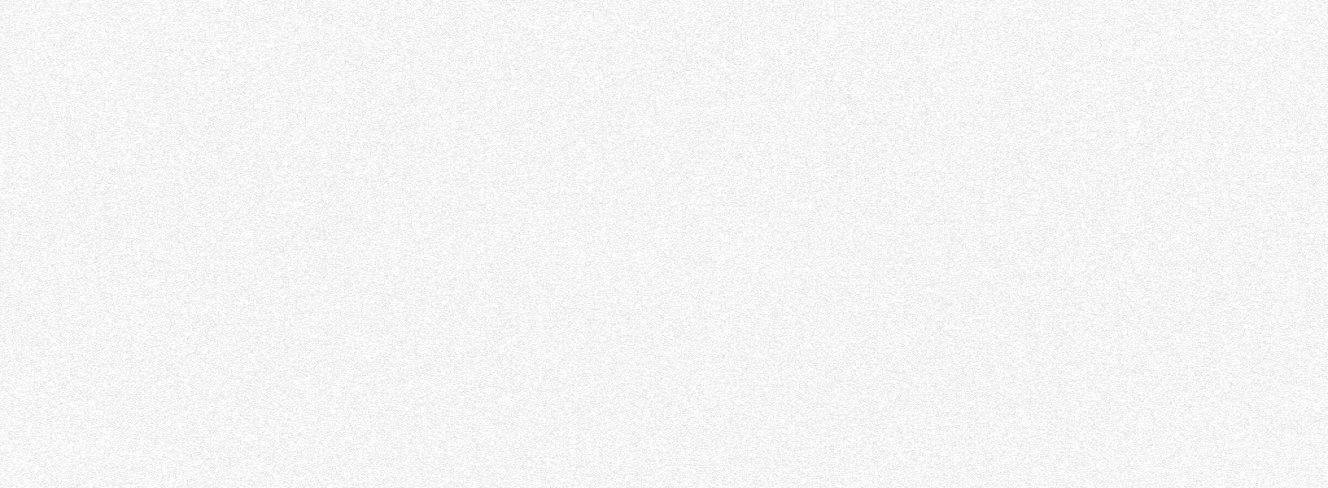