Taylorism
Taylorism - named after its inventor - refers to the work organization method developed by American engineer Frederick Winslow Taylor at the end of the 19th century, and systematized in his book The Principles of Scientific Management (1911).
A veritable scientific tool in the service of productivity, Taylorism methodically reorganized work by breaking down and optimizing the distribution of tasks.
The context of the Industrial Revolution
Taylorism developed in the macro-economic context of the Industrial Revolution, synonymous with the appearance of the first very large-scale factories. Unable to copy the operations of individual workshops, which were subject to immense productivity demands, industries were forced to rethink their production techniques in depth.
For a long time, the division of labor and its standardization were widespread intuitions in response to these new realities. However, Frederick Taylor went even further in this direction, modeling this optimization of work in a perfectly methodical way.
Vertical and horizontal company reorganization
First and foremost, Taylorism imposed an initial - vertical - reorganization of the company, with a dissociation of decision-making and execution activities. According to Taylor, tasks should not be designed by those who will carry them out. Engineers were responsible for organizing their factories and allocating tasks, while the role of workers was simply to implement decisions imposed on them from above.
The second reorganization of work is horizontal: the division of tasks on the production line. According to Taylor, this reorganization must be carried out in three stages. First, all activities on the production line must be broken down into a precise number of simple, identified tasks. Then - and this is the most scientific part of the method - the most efficient gestures, movements and operations for each task must be determined as objectively as possible. This is Taylor's obsession with the One Best Way, the central pillar around which his entire method is built.
Finally, it is necessary to define the optimal matrix (the set of all the best ways) to optimally combine all the company's resources, i.e. man, capital and material.
Unleash your organization's potential.
We're here to answer all your questions and support you in your projects.
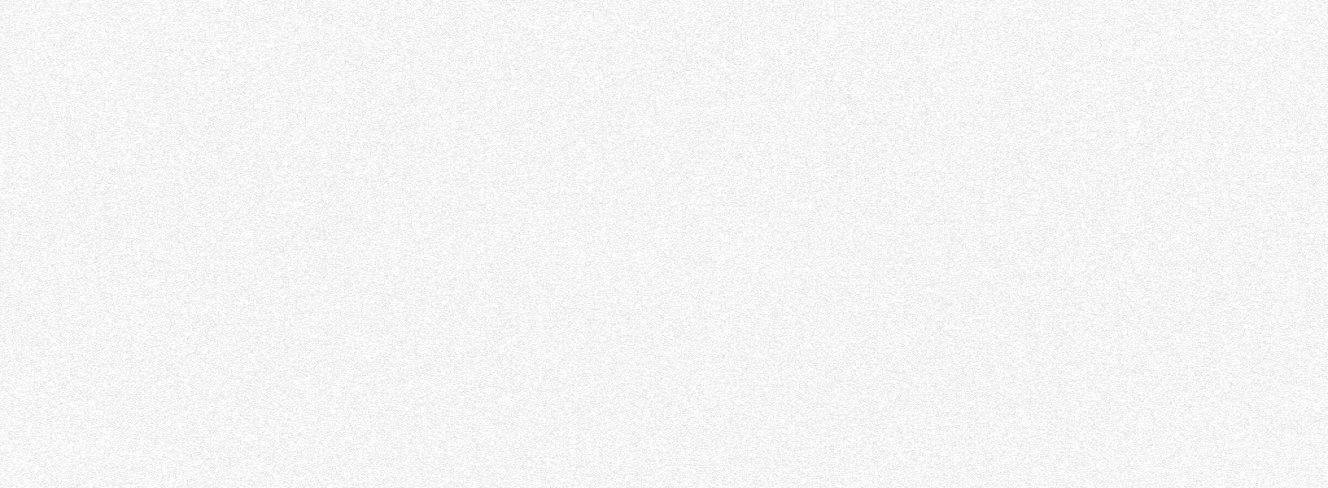